Many people have been stuck when they want to transport heavy materials from one place to another. With discoveries in the market conveyor systems were invented to aid in the transportation of materials; these systems are mechanical. Materials are moved from one place to the next through rollers, conveyor belts, or wheels. The powering systems are done by gravity, manually, or motor devices. There are several varieties of handling systems of different materials depending on the materials’ nature in question. Various businesses like MAINWAY HANDLING focus on manufacturing and delivery of transport services.
Important specifications of conveyor systems
1. The unit length and the loading capacity
Manufacturers offer the specific attribute when the conveyor system is built with a custom length, allowing users to determine the loading’s relevant margins.
2. The maximum loading capacity
It is also referred to as the flow rate and is associated with the load capacity placed per unit length. Manufactures clearly state the amount of load occupied per every fixed length on the purpose-built conveyor systems.
3. The rated speed
The rate used in speed terms is ft/min in the belt conveyor systems. The powered roller conveyor systems describe the velocity in linear terms depending on the units packaged, or cartons moved over the system rollers. Speed rates also apply in the salt and chain conveyors.
4. Throughput
It is used when measuring the capacity of a conveyor when handling powdered and bulky materials. The capacity is often given as the volume produced per unit time, for example, the cubic feet produced per minute. The kind of attribute is applied to the bucket, vacuum, vibrations, walking beams, and screw conveyor systems.
5. Configurations of the frame
It refers to a conveyors’ system shape. The frames are of different shapes, for example, curved straight or the z-frame.
6. Drive locations
They are located in different areas within the conveyor system. At the discharge conveyor side, the head drive is located there and is commonly found in the systems. The center drives, at times they are not always located at the center of the conveyor systems, but at times they are placed along the conveyor’s length. There are drivers located underneath the conveyor systems, and all the drivers are used when reversing the conveyor direction.
There are several types of conveyor systems in the market: rollers, belts, powered rollers, slats, ball transfers, magnetic buckets, the chute, verticals, walking beams, wheels, and vibrating types.
The belt conveyor systems
They handle materials using continuous belts in conveying materials, and it is extended in endless loops between two end pulleys. Either one of the two ends has underneath them a roller. The belt system is supported by a metallic pan slider or very light loading, and friction has no friction to ensure that the belt is not dragged on the rollers. They are powered by motors using constant or variable gears for speed reduction. Conveyor belts are made from leather, plastics, metals, fabrics, or rubber. They are either inclined or horizontal, and the belt systems are strengthened depending on the load’s capacity to be transported.
Roller systems
Gravity or manual labor is used to convey products; the frames use parallel rollers. They are used in handling materials in the assembly lines and the loading docks. Depending on the floor space available and application procedures, they are either curved or straight lines. The roller conveyor systems specification is the center axle dimensions and the diameter of the rollers, among others.
The powered roller conveyor systems
They use frames mounted with powered rollers to convey materials. They are mainly used when handling materials and products requiring powered conveying of the materials. They are used by various companies when handling their food products, packaging, and steelmaking processes. The drive used includes chains, motored rollers, and belts. Also, the important specifications are; diameter of the roller, roller material, dimension of the axle center, and drive types.
Considerations of system selections
The most important consideration to make when selecting a system is the material to be conveyed. Other considerations include; temperatures, level of abrasion, corrosiveness, size of the materials, nature of materials, and the products’ water content. When handling the systems, the feeding time is a sensitive issue, and it requires precision compared to the conveying process. A conveyor system’s choice also considers its operating environment, for example, the humidity levels, temperatures, pressure, vibrations, and the kind of product being handled. The room available in the workspace determines the size of the installed conveyor system and its compatibility with the available equipment.
There are several advantages associated with the conveyor systems, including;
Reduced waste
Conveying heavy materials in a production line is conveniently done as manual labor is not required. Companies that focus on handling heavy materials with human labor suffer manual wastage, which increases production costs. People are more prone to physical injuries than the machinery as their safety is not always promised. If you want to reduce such incidence, use automated conveyor machines, which require minimal human labor. The systems speed up a plant’s production process, which in turn increases profits. The human labor used in transportation is used to cover other important factory tasks.
Flexibility
They help achieve the ultimate flexibility required in plant operations, and they are used at any time whenever necessary. When purchasing a conveyor system, ensure you choose the one that perfectly fits all the operations, including transportation and the final storage process to the final destination. Some systems accommodate several products in a single line of production.
Quality control enhancement
Automated conveyor systems improve the quality controls, and they eliminate the scarps in production. They detect any issues in a product, for example, faulty parts or excess metal. They help reduce time wastage to handle the production process from the first to the final stage. High-quality inspections by the machines ensure that only quality products are ready for consumer consumption. Before deciding on installing conveyor systems in the industry, ensure expert consultation to ensure the right selection and relevant technologies for efficient operations.
In conclusion, conveyor systems help the handling of materials in the transportation and production process. Their efficiency in handling products ensures quality control, workers’ safety, flexibility, reduced wastage, and proper time utilization. Always enquire from the experts the relevant selections of systems that effectively work within the industry environment.
What Is Your General Understanding Of The Conveyor Systems?
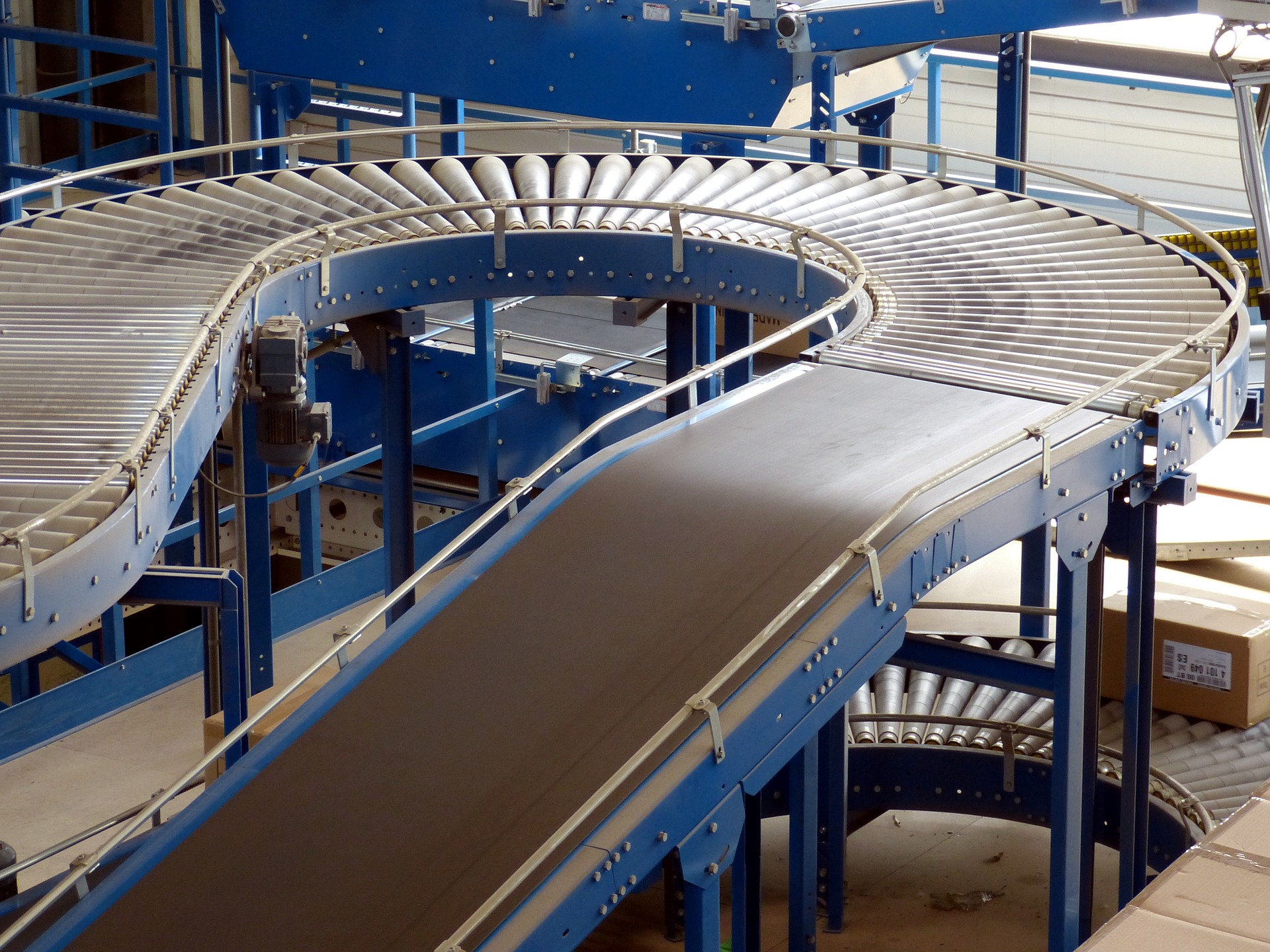
Source: pixabay.com